Know-how
This is what the name REISSMANN stands for.
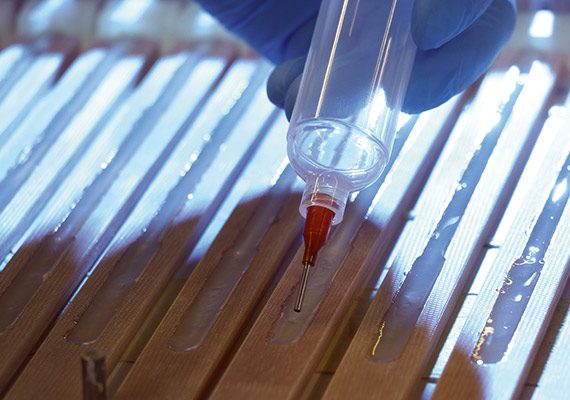
Metering and potting technology
More than 30 years of experience guarantee the highest quality standards. Our experienced team has mastered metering and potting technology at the highest level. Our design engineers build, develop and continuously improve devices and process aids in close cooperation with our employees.
Soldering technology
The ergonomic and optimised workplace design increases the efficiency of work processes. The soldering tables have been specially designed and built to meet our requirements.
Temperature settings of the soldering equipment and soldering tips are electronically / digitally preset – we ensure our high quality standards in all processes. Solder types are process-specific and standardised. The output of solder and primary materials is controlled and secured by the tool output.
All successive work steps are checked and safeguarded by quality windows. The latest innovation in the soldering division is our soldering robot, where solder joints are soldered in a fully reproducible manner with consistent settings (temperature, solder quantity, etc.) every time.
Our soldering technologies: Soldering robot, solder wave machine and manual soldering

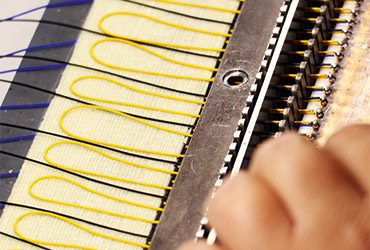
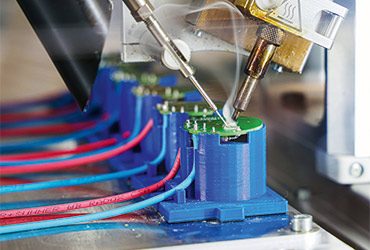
Temperature sensors
Industrial technology is particularly challenged in all areas where harsh environmental conditions prevail. This applies to external systems in energy technology, conveyor and lifting systems, and in robots used in production facilities. It goes without saying that the efficient use of technology demands maximum availability. It is vital that every “link in the chain” remains stable at all times.
Heavy duty: Because drives have to keep a “cool head” even in harsh operating conditions.
Downtimes are costly. Interruptions due to signs of wear are virtually unavoidable, in particular in harsh operating conditions. They are accepted – albeit begrudgingly. As a general rule, wear affects those components that come into direct contact with the harsh mechanical influences. And that is calculable.
Reliable actual temperature values are required.
Unforeseeable disruptions, on the other hand, result in significantly higher costs. These include drive failures due to thermal overload. As such, temperature sensors provide crucial data for monitoring thermal drive conditions and therefore form a reliable basis for a prompt response.
The monitoring sensors in systems that operate under harsh environmental conditions must be designed to be just as robust as all other components.
Temperature sensors: Heavy duty and highly sensitive.
Robustness and precision in the recording of measured values, coupled with functional reliability even under high loads – at first glance this seems like a contradiction in terms, but it reflects the demands that harsh operating conditions place on temperature sensors.
Very high pressures sometimes occur – at the corresponding measuring positions of high performance drives (for example in the windings of coils), which require high mechanical resistance from the sensors. This applies not only to the transducers, but also to their supply lines. Pressure-induced constrictions can lead to insulation breakdowns. Reliable actual value recording would then no longer be guaranteed.
Temperature sensors from REISSMANN Sensortechnik GmbH for use under harsh operating conditions.
REISSMANN has developed its temperature sensors for use in electrical drive technology for wind turbines, for conveyor, lifting and robot systems, and for industrial trucks based on a requirements profile derived from practical experience:
- Effective protection, e.g. against the glass encapsulation of the PT elements breaking
- Internal sensor design based on the spreading resistance principle
- Supply cable protection against highly constricting winding wires and high pressures
- Optimised temperature transmission due to low thermal time constant
- Resistance to aggressive gaseous and liquid media
- Insulation resistance up to 8000 V AC in accordance with DIN EN 50178
Close cooperation with users and with component and cable manufacturers has resulted in temperature sensors that reaches all standards of the defined profile at an optimal price-performance ratio.
REISSMANN sensors are outstanding for their consistently high precision and long service life, and they retain their effective linear characteristics even under harsh environmental conditions. The highly notch-resistant reinforced insulation of the supply cable ensures high resistance to aggressive media. Additional special high voltage-resistant, reinforced double insulation prevents damage to the outer insulation sheath by constriction of the winding wires and the resulting pressures.
Extensive field applications attest to the quality: The PT / PTC / NTC sensor systems have proven themselves in practice.
Prior to series production, REISSMANN’s temperature sensors were subjected to extensive testing in the field.
Renowned commercial users that REISSMANN succeeded in involving this test phase registered no malfunctions whatsoever. The guaranteed properties remained constant even under harsh installation requirements.
All of our sensors can be produced in high volume. They are successful in winding and bearing monitoring, as well as in carbon brush holders of drives in a wide range of applications including saline cleaning processes or difficult climatic conditions, such as high humidity and temperatures between -50 °C and +260 °C.
Specially protected production and testing zones and qualified specialists ensure consistently high production quality.
The manufacture of certain types of sensor / modular design requires a particularly secure process that includes effective protective measures.
Key term ESD: (Electrostatic Sensitive Devices)
The entire production and testing area is equipped and labelled as an ESD protection zone in accordance with DIN EN 61340. Electrostatic conductive floor coverings and furniture systems, centrally earthed, prevent electrostatic damage to goods at risk.
The earthing concept also consistently includes all individuals present in the correspondingly marked areas.
Regular checks, performed with appropriate measuring equipment, ensure the effectiveness of these facilities and systems. Ongoing training courses keep the qualifications and expertise of employees in these sensitive production and QA areas up to date at all times. The quality assurance concept also integrates those stations that follow the final inspections – with appropriate storage facilities, packaging materials, transport and dispatch equipment.
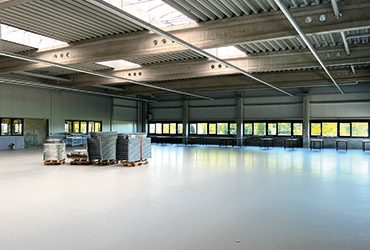
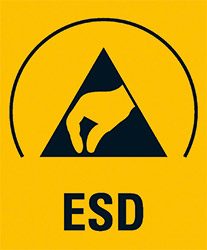